Advanced Manufacturing, Equipment & Processing Capabilities
Our commitment is to meet and exceed customer satisfaction through our advanced equipment and processing capabilities of foam materials. We achieve this by utilizing our own modern converting equipment, adhering to ISO 9001:2015 & AS9100:2016 standards, committing to continuous improvement to enhance quality and contain costs, and investing in Soundcoat owned and operated manufacturing facilities on both the East and West coasts for optimal flexibility and speed. We supply materials to your specifications, which can be ordered in sheets, rolls, or buns across a wide range of thicknesses and configurations.
Our lineup of advanced manufacturing equipment includes a broad array of foam converting capabilities, lamination of materials for composite creation, and custom foam molded parts. Additionally, we offer manufacturing process capabilities including personalized kitting, line sequencing, JIT, Kanban, and a variety of precise, high touch finishing processes including clean room manufacturing, hydrophobation, and exclusive edge sealing.
Water jet cutting
Water jet cutting results in finished parts with pin-point precision. Our “Made in America” 5-axis water jet machines enable the manufacture of complex shapes and manage taper angle control, giving you incredible versatility in the variety of parts we can manufacture.
Advantages:
- Ultra-precise
- Fast and efficient
- Versatile to cut a multitude of materials (wording to be refined)
- Ability to cut large parts versus other cutting methods
- Smooth, clean edges
- Use of nesting programs result in minimal waste
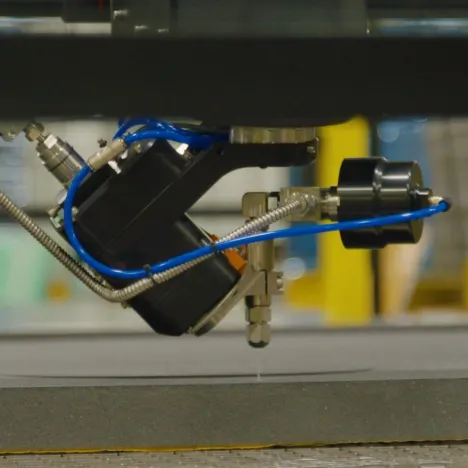
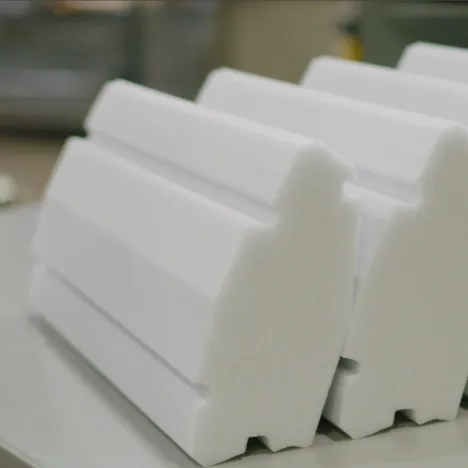
Horizontal contour cutting
For three-dimensional part needs, this specialized process creates precise and complex shapes, curves, and profiles in foam. First, your design is translated into our CAM software. Then material is loaded onto the cutting table and an oscillating blade moves rapidly back and forth through the foam block, following the design provided. After the cutting is finished, the foam parts are removed and inspected.
Advantages:
- Precise
- Versatile (many foam types & densities)
- Curved & straight cut capability
- Efficient use of material & production time
- Scalable (automated processes, high production speed and repeatability)
VERTICAL cutting
A fully-integrated, CNC vertical cutting machine suitable for a wide range of materials, including various types of fabric, foam, and even some non-textile materials.
Advantages:
- Continuous cutting
- Consistent speed
- Accuracy & control
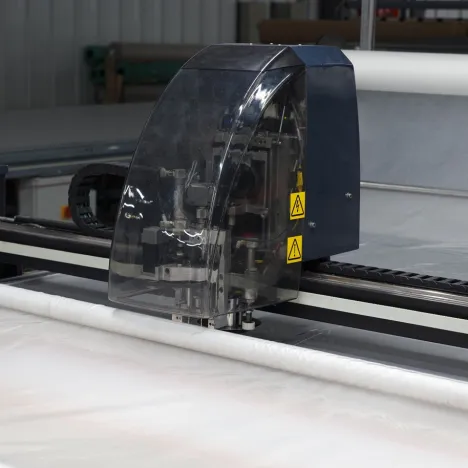

Die cutting
Die cutting begins with your part’s design. We create the die based on your design, which is used to cut the foam to your exact specifications. The die is mounted onto our flatbed press, the foam is aligned with the die, and then the hydraulic press is lowered over both elements creating the cut parts.
Advantages:
- Precise
- Versatile (open & closed cell, high density)
- 4-plane, straight cut capability
- Consistent
- Cost-effective
Foam sheeting
Specialized sheeting machinery is used to slice foam buns into sheets of uniform thickness. Our machine quickly and automatically can cut sheets to as little as X inches (X mm) thicknesses.
Advantages:
- Uniform
- Consistent
- High-quality
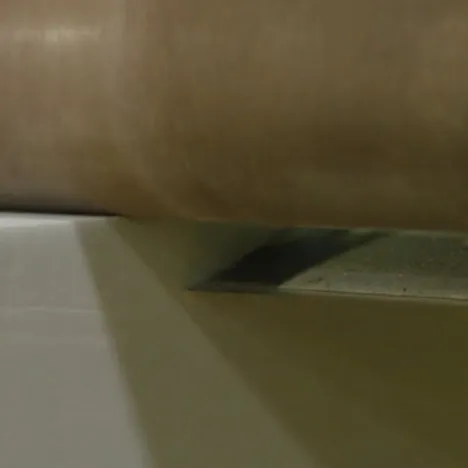
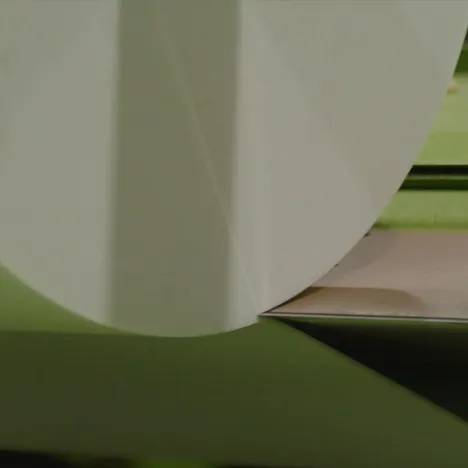
Foam skiving
This precise mechanical process reduces the thickness of foam to specific levels, shapes, or profiles. Foam is fed into the machine and the blade is adjusted to the desired thickness. The blade rotates over the surface of the foam, removing layers in the desired thickness.
Advantages:
- Precise
- Versatile (thin sheets & complex profiles)
- Consistent results with minimal waste.
- Customization
Guillotine cutting
Achieve straight edge-to-edge cutting to your specifications with our hydraulic powered guillotine cutting machine.
Advantages:
- Clean and accurate cuts
- Optimized product usage
- Custom sizes
- Durability and reliability
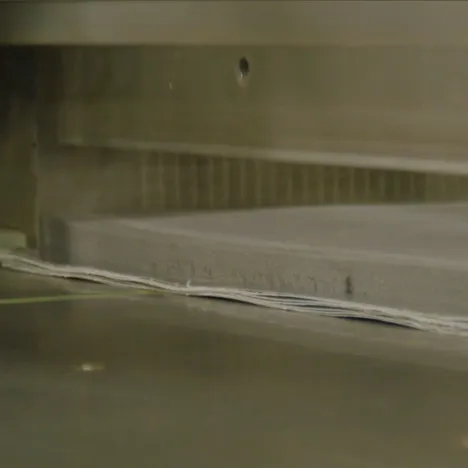
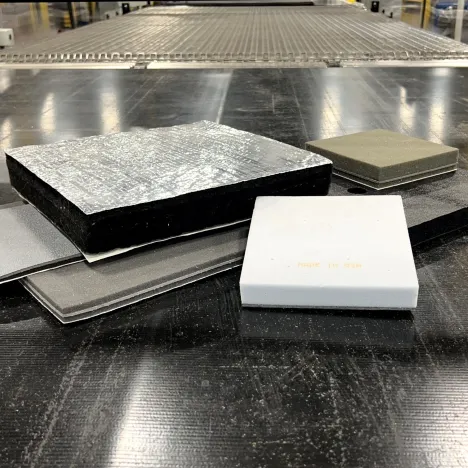
Film & composite lamination
Used to enhance the properties of foam by adding layers of films and/or composite materials, lamination can improve the foam’s durability, thermal insulation, damping or gasketing abilities, strength, or appearance. We employ several lamination methods for creating composite materials including hot roll, flatbed, and hot melt.
Advantages:
- Enhanced foam properties
- Custom composite creation
- Diverse processes for optimal product performance
Clean room
Our clean room allows us to manufacture parts for the aerospace and microchip processing industries in a temperature, humidity, and particulate controlled environment. It all starts with the design of the room itself – smooth surfaces and materials that do not shed, zoning areas, and airflow control. We follow entry protocols and have environmental controls to maintain stable levels of temperature, humidity, and air pressure. We employ strict cleaning, material handling, and equipment maintenance standards, and follow regular monitoring and validation schedules to ensure standards are maintained.
Advantages:
- Precise manufacturing
- Reliable performance
- Standards adherence
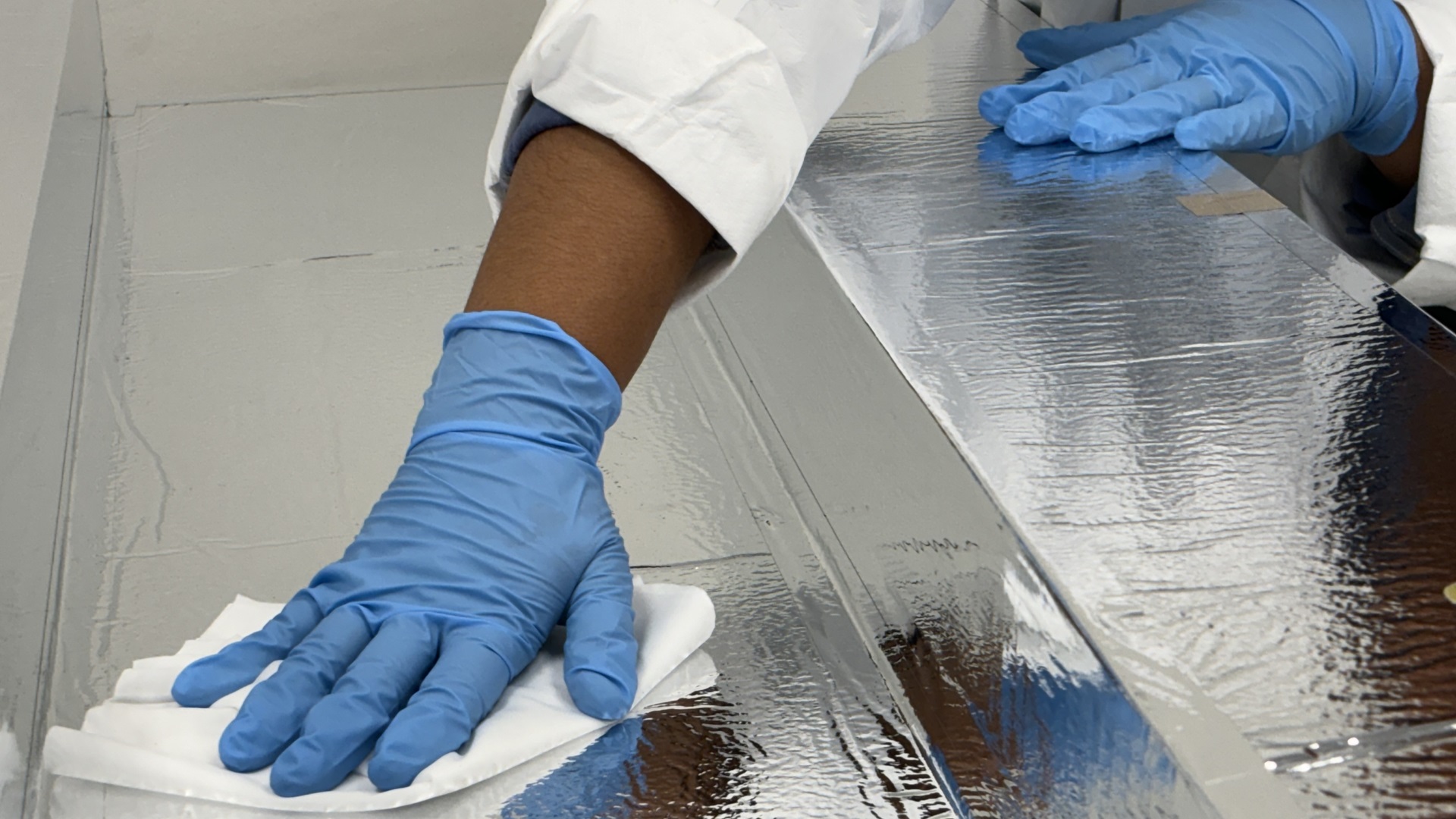
EDge sealing
Uniseal is our proprietary process of polymer edge sealing that fully-encapsulates cut foam pieces without seams, while retaining acoustic performance. It prevents fraying or contamination from dust and is excellent for protection in high moisture areas.
Advantages:
- Protection from contaminants and moisture
- Aesthetic enhancement
- End-use versatility of foam
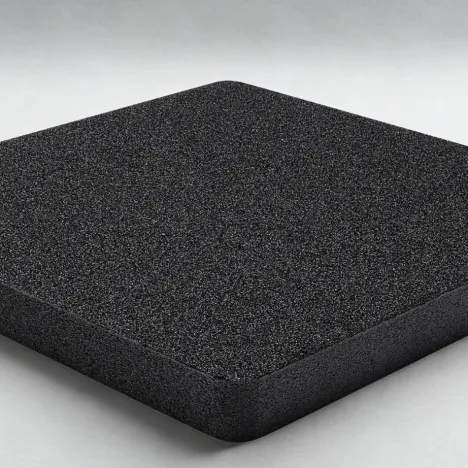

Hydrophobation
Our hydrophobation process is essential for applications where water-repellency and/or oil-repellency are paramount, such as aerospace and aviation. Melamine foam is fully immersed in a hydrophobic agent to ensure the water- and oil-repellant qualities are retained after the foam is cut to shape. Then we cure the foam to stabilize the hydrophobic agent and finalize the process by cutting the foam to your shape.
Advantages:
- Water repellant
- Oil repellant
- Enhanced durability
- Improved performance
CABFOAM®
Cabfoam® is the name for an exclusive Soundcoat finishing process. What started as a way to improve the look of foam installed inside operator cabs, evolved to become name by which we refer to the finishing process, “Cabfoam”. It process begins by selecting a polyester based polyurethane film (usually Soundfoam O or Soundfoam M). Then a matte PU film is placed on the front surface of the foam, which is then fed through a type of laminating machine that embosses the film and a honeycomb pattern onto the front surface of the foam.
Advantages:
- Visually appealing
- No impact on sound absorption
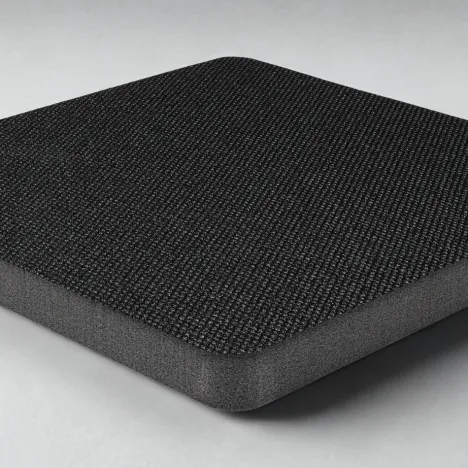
CUSTOM Foam molded parts
Looking to prevent noise and vibration before your product goes to market? Explore custom foam molded parts by Soundcoat. For original equipment manufacturers (OEMs), molded parts have infinite applications, but always result in the same outcome: quieter performance from the beginning.
By partnering with your product design team, we can build foam parts that require no adhesives or fastener, yet fit your products exactly. The process is simple; using your product designs, we fabricate the metal mold. Raw foam material is prepared for molding and can be modified with additives to enhance flexibility, strength, or flame resistance. Finally the foam is injected into your mold. Once the part is approved for production, your foam molded parts are produced quickly and efficiently.
Advantages:
- Complex shapes
- Lightweight & durable
- Improved material efficiency
- Customizable material for exact fit and function
- Enhanced customer satisfaction
We can also help with improve sound quality through our revolutionary Soundcoat 360 Solution™.
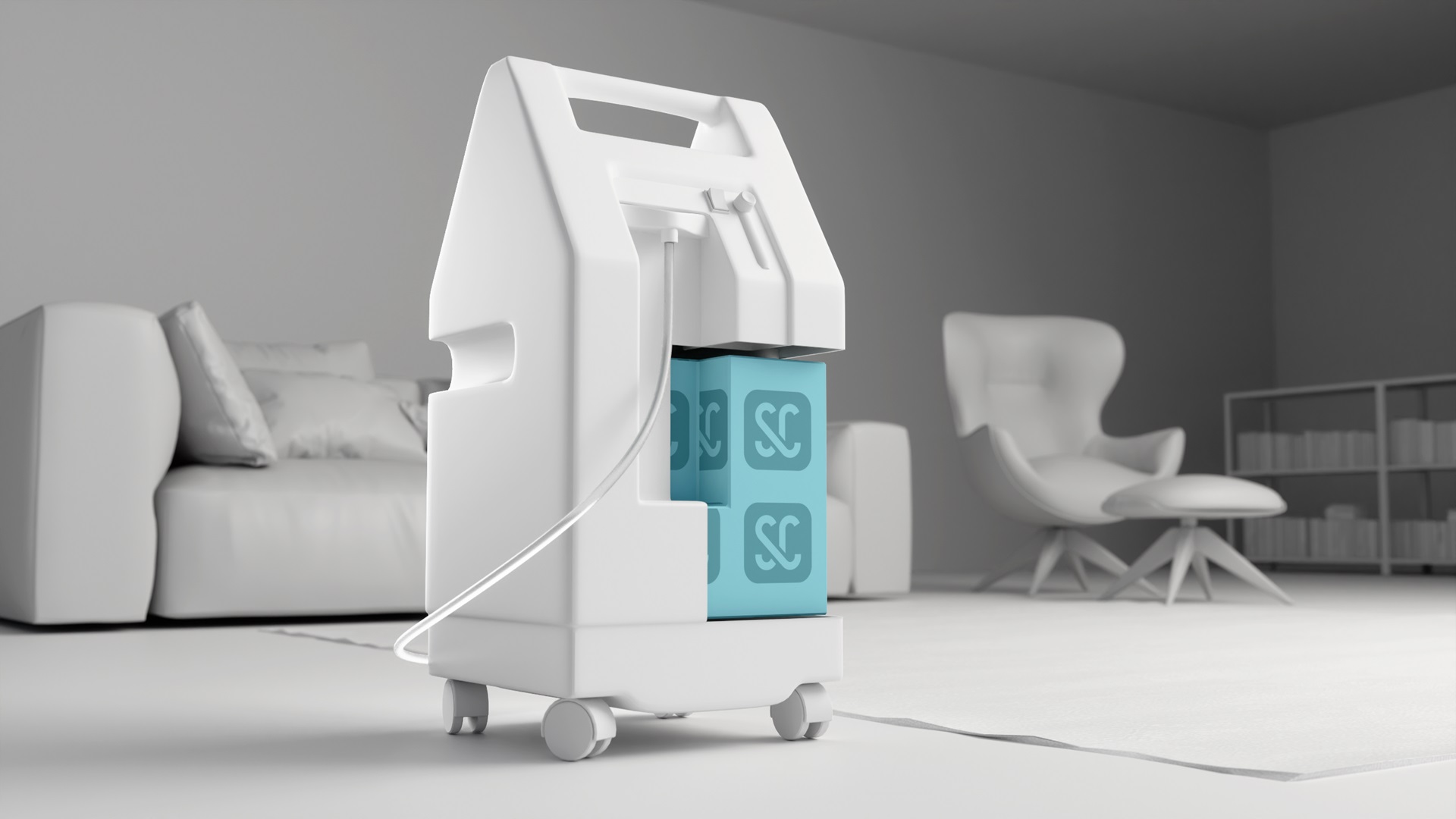